وظائف تنقيب الاردنوظائف في الاردن
QA/QC Manager
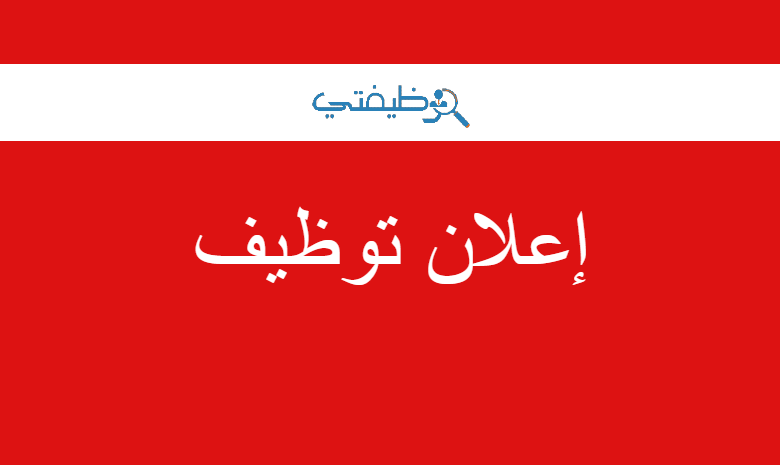
Role Objective:
Assuring consistent end product quality by developing and enforcing good quality management system across the entire process. Responsible for the testing and inspection function of the factory, as well as supervision of the employees who perform that work, compiling and analyzing data and measurements to help management improve the firm's work and manufacturing processes.
Detailed Roles & Responsibilities:
STRATEGIC:
- Provide the planning and leadership to the QA/QC Department by ensuring that the appropriate structures, systems, competencies and values are developed in order to meet and exceed the goals of the QA/QC plan.
- Assume overall responsibility for developing the annual QA plan for the organization.
OPERATIONAL:
- To develop and document a company-wide quality assurance system in according with the standard with the cooperation of all concerned departments. This will include setting up the overall policies, strategies and procedures related to quality assurance activities, documenting them in a satisfactory manner and making them in known throughout the company.
- To organize and manage the quality control activities including the followings:
- Control of incoming material quality.
- Control of in-process quality, including all related machines, tools and operators and products. In- process inspection in cases where non-conventional measuring with means or special cases in the quality control lab are needed.
- Final inspection on finished products; assemblies, sub-assemblies and components.
- To work towards a positive and active awareness of quality and transforming quality and integrating it with the overall culture of the company.
- To follow new and changing products, processes and practices with a view to quality and to advice parties responsible for deficiencies in quality and to suggest measures which will lead to reduce quality cost.
- To establish and head the company’s quality council (for discussion and decision on all important quality matters, organizational objectives, quality polices and plans).
- To ensure that produced quality is as per designed specification and reporting in the adjustment of quality.
- To lead the implementation and documentation of a companywide assurance system in accordance with ISO 9001 series of standards.
- Gauge keeping, checking and calibration.
- To lead the assessment of quality requirements and manufacturing determinants and to collect data necessary to carry out capabilities' studies.
- To oversee relevant quality training programs for all departments of the company.
- To ensure that work is carried out in accordance with the policies laid down in such a way that the objectives are reached.
- Overseeing the organization of the Quality Control Section, including internal procedures and communication with other departments.
- Ensuring that work procedures in all departments are in line with ISO expectations and the Company QMS system. Also, ensuring that proper coordination with other sections is done to synchronize all company activities related to job orders and others.
- Manage QA/QC operations smoothly and ensuring that the QA/QC department tasks and projects are completed in time.
- Ensuring product quality strictly followed as per the appropriate standards and certifications of the product line.
- Development and management of system for workflow to maximize efficiency and minimize errors in QC.
- Overseeing the establishment & standardization of QC procedures & documenting them.
- Continuous training & development and cross training of QC technicians and personnel. Establishing a system of training and preparing inspectors to perform on-the–machine inspection, in-process inspection, and if required supporting field technicians at client venues.
- Continuously supporting the Manufacturing Department and other technical departments in trouble shooting of in-process or assembly problems to help in overcoming such problems in the most economical way, without compromising on the quality.
- Overseeing the maintenance of QC section resources available for QC staff at all times, including computers, data libraries, internet access, etc…
- Upgrading QC staff knowledge and general awareness and culture emphasizing quality and efficiency.
- Overseeing the scheduling of QC job work is in coordination with production management in order to ensure smooth factory operations.
- QC research and development for the purpose of continuous improvement in methods, computer software, and latest benchmarks and available technologies in QC & inspection.
- Ensuring smooth QC Section administrative tasks with coordination with HR by keeping track of personnel attendance, commitment, & conduct at all times.
- Development & management of relevant technical and administrative procedures & its documentation within the section.
- Development and management of system for handling, storage, archiving and backing-up of all QC data.
- Protects organization's value by keeping information confidential.
- Other duties and responsibilities as assigned by the Management.
- Having the depth knowledge of fiber technologies and network applications.
PEOPLE MANAGEMENT:
- Oversees the responsibilities and duties of all employees in the QA Function.
- Responsible for the training and development of personnel in the QA Function.
Other duties and responsibilities as assigned by the Management.
Educational Qualifications:
- Master’s or Bachelor’s degree in Industrial Engineering or a related field is preferred.
- Lead Auditor Certification for ISO 9001:2015 (IRCA Approved Auditor).
Experience:
- Minimum of 10 years.
Behavioral Skills:
- Customer orientation, professional development, teamwork, leadership, process and execution excellence.
Technical Skills:
- Computer skills and communications skills in English language (read, write and speak).