Factory Manager
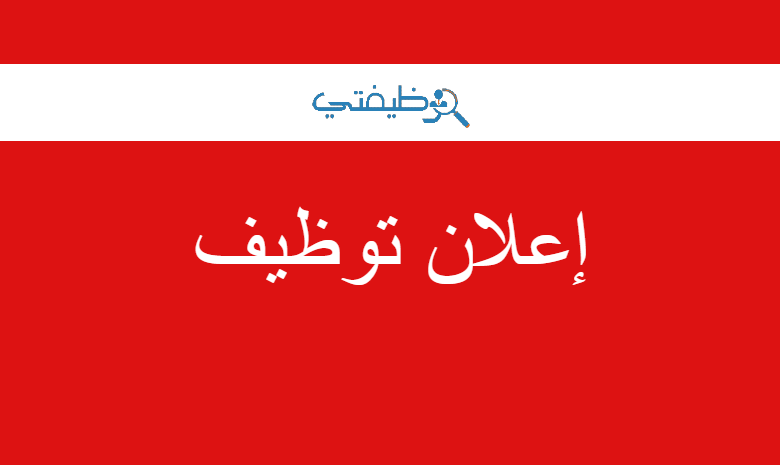
Factory Manager
الوصف الوظيفي
JOB PURPOSE:
The Factory Manager shall be responsible for general supervision of all Departments of the Factory including R&D, Technical, Planning, Production, Quality Control, Maintenance and Industrial Project Sales. The Factory Manager oversees every activities in a plant. They are to implement all rules and policies to all factory workers and ensure them that they follow ever regulation
SCOPE:
Factory Manager reports to the General Manager of the Company. The Factory Manager oversees every activities related to the Factory Division. Responsibilities also include recruiting, hiring and training personnel and facility/physical plant up-keep and capital improvements. In addition, the Factory Manager will be responsible for annual budget planning and execution. They will work closely with the production team to increase productivity and profitability within the manufacturing operation. The Factory Manager shall ensure that safety regulations and policies are implemented among the factory workers. The Factory Manager shall also ensure good relationships among the workers and that there are equal treatment applied to them
ROLE RESPONSIBILITIES:
- Provide leadership for the successful day-to-day operation of the facility.
- Review established production schedules for all manufacturing departments to insure established inventory levels are met while operating at the highest efficiency possible.
- Ensure Raw materials and components are Purchased on an optimum manner.
- Maintain Inventory levels and control flow of Raw Material & Components to Factory floor. ∙ Work closely with Technical Department/Estimation to determine trends and areas of improvement ∙ Research ways to reduce costs while maintaining product quality.
- Liaise with Sales Department to understand the market need and develop new products, as per Sales recommendation, to meet the market requirements.
- Communicate with research and development as well as product management personnel to develop new product strategies
- Work closely with quality personnel to review product consistency.
- Ensure scrap rates are to the minimum.
- Coordinate the hiring and training of all manufacturing personnel.
- Monitor operation expenses.
- Develop and execute the Factory budget in consultations with various Departments. ∙ Analyze workforce requirements.
- Conduct performance appraisals and provide coaching and guidance to all operations employees. ∙ Encourage and promote operating in a continuous improvement environment.
- Remove production constraints; allocate human and equipment resources and direct production employees to attain all established goals.
- Remove waste and constraints from the production process to improve efficiencies and enhance productivity.
- Work with Purchasing Manager to develop and improve supplier relationships.
- Approve purchase requests and route it to Purchasing Manager to place orders.
COMMUNICATIONS AND RELATIONSHIPS:
Internal: Manager, Supervisor, Colleagues and staff down the line
External: External Companies, Clients etc.
WHO DOES PERFORMANCE REVIEWS FOR THIS ROLE?
General Manager
KEY PERFORMANCE INDICATORS:
- Improving Customer Experience & Responsiveness
On-Time Delivery to Commit
Manufacturing Cycle Time
Time to Make Changeovers
- Improving Quality
Yield
Customer Rejects/Return Material Authorizations/Returns
Suppliers Incoming Quality
- Improving Efficiency
Throughput
Capacity Utilization
Overall Equipment Effectiveness (OEE)
Schedule or Production Attainment
- Reducing Inventory
WIP Inventory/Turns
- Reducing Maintenance/Preventative Maintenance (PM)
Percentage Planned vs. Emergency Maintenance Work Orders
Downtime in Proportion to Operating Time
- Increasing Flexibility & Innovation: Continuous Improvement
Rate of New Product Introduction
Engineering Change Order Cycle Time
- Reducing Costs & Increasing Profitability
Total Manufacturing Cost per Unit Excluding Materials
Manufacturing Cost as a Percentage of Revenue
الوصف الوظيفي
المهارات
KNOWLEDGE, TRAINING AND EXPERIENCE REQUIRED FOR JOB
Education: Minimum educational qualification: Bachelor's Degree in Electrical Engineering
Experience
- Minimum educational qualification: Bachelor's Degree in Electrical Engineering
- 20+ years progressive experience in a key leadership/management role at a manufacturing facility preferably Switchgear Industry.
- Previous experience/strong understanding of budgeting/expense management with a basic understanding of financial and accounting practices.
Language skill:
Strong command of English for communicatng. Arabic is an additional advantage.
Other skills & competencies required:
- Demonstrated strong leadership, team building and advanced coaching skills. ∙ Demonstrated ability to motivate people, assess and develop employee skills. ∙ Demonstrated understanding of the principles and applications associated with manufacturing operations, maintenance and engineering.
- Excellent interpersonal communication and listening ability.
- A strong ability to be adaptable and flexible.
- Strong analytical and decision-making skills.
- Ability to work with teams and lead decision-making processes in a team environment.
- Highly motivated, results oriented, driven.
Working Conditions: The working environment of a Factory manager is both in an office and in the factory/ plan.. Factory managers may work beyond the basic working hours due to some work related tasks that are needed to be done in a day.
المهارات
تفاصيل الوظيفة
- منطقة الوظيفة
- الكويت
- قطاع الشركة
- البيع بالتجزئة وبالجملة
- طبيعة عمل الشركة
- صاحب عمل (القطاع الخاص)
- الدور الوظيفي
- التصنيع
- نوع التوظيف
- دوام كامل
- الراتب الشهري
- غير محدد
- عدد الوظائف الشاغرة
- 1
تفاصيل الوظيفة
المرشح المفضل
- الجنس
- ذكر