Senior Engineer, Maintenance Optimization (UAE National)
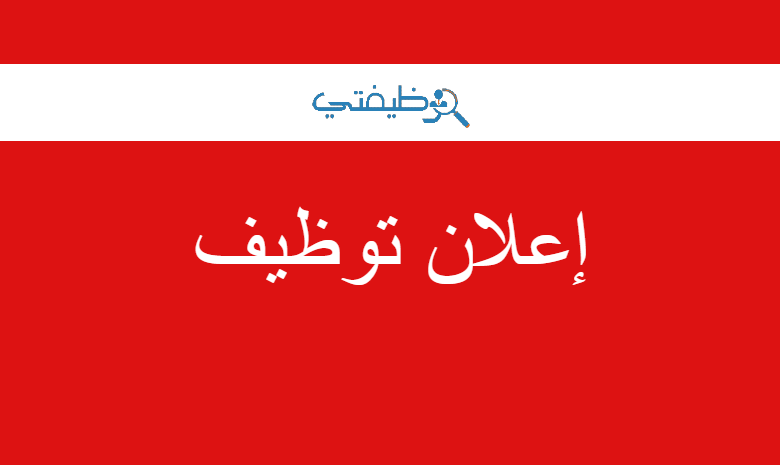
Senior Engineer, Maintenance Optimization (UAE National)
الوصف الوظيفي
3. JOB PURPOSE:
Formulates the maintenance strategies for the assets upfront during engineering stages. Ensures maintenance is carried out in accordance to international standards and practices through the preparation and implementation of maintenance optimization programs in order to achieve the ultimate availability and reliability of the equipment. Sets, control and implement specialized maintenance optimization, reliability and management systems and methodologies.
4. KEY ACCOUNTABILITIES:
- Provides advice and assistance to Maintenance Departments in determining reliability objectives, developing reliability systems and procedures for the maintenance / overhaul of equipment to achieve optimum performance and reliability.
- Manages and review equipment criticality databases to ensure that the relative importance of each piece of equipment.
- Develops, implements and follows-up of specific reliability programs related to Maintenance Optimization based on defined Company reliability strategies. Performs periodic reviews of maintenance strategies with regard to preventive / predictive maintenance programs and recommends enhancements, such as, developing and proposing cost effective changes from Time Based Preventive Maintenance (corrective, breakdown, preventive) to Condition Based Monitoring (predictive).
- Implements a reliability cantered maintenance (RCM) approach to identify the necessary maintenance tasks for the critical assets to avoid over / under maintenance.
- Assist, consult and coordinate with and between field on the problems and practices in order to Standardizes Maintenance Standard Procedures and Practices.
- Follows the policies and guidelines to achieve target plant availability & reliability figures.
- Liaises with Engineering & Projects and assists in plants and equipment reliability issues, reliability design engineering during all the phases of engineering and construction.
- Serves as technical resource for Reliability Tools; life data analysis, RAM, Weibull. AMSAA, SPARC. Uses reliability techniques and software to perform reliability modelling on equipment and process units to identify focus areas for reliability, availability, and maintainability improvement.
- Builds up a library of Failure Mode and Effect Analysis (FMEA) for different equipment in the area of responsibility to assist operations / maintenance personnel to overcome different types of problems.
- Carries out specialized reliability studies as needed and provide recommendations for improvement to reach the recommended values.
- Builds the adoption and use of good failure coding practices (using ISO14224) in cooperation with the Maintenance Planning & Scheduling. Responsible to perform statistical analysis on machinery failure data and work order closing codes.
- Leads and facilitates root cause analysis (RCA) of major / critical equipment or the repetitive minor / critical equipment failures, recommends solutions, and follow-up on implementation.
- Participates in the preparation of maintenance KPI’s and reports to allow for better analysis of both maintenance practice & assets performance.
- Supports Senior Material Engineers for analysis of spares usage and failure data to determine proper stocking levels.
- Assists Maintenance Engineers with reliability analysis of proposed equipment modifications. Makes specific recommendations to improve machinery performance and reliability based on analysis of process and failure data.
- Controls / extends the existing condition monitoring system to monitor assets’ condition from different perspectives to capture symptoms of deterioration in early stages to avoid harmful consequences.
- Directs the data collection team to carry out the routine condition monitoring tasks or any other related activities as and when required within the area of responsibility.
- Coordinates the issues of the Field Data Integration System project FDIS with CITD.
- Participates in the review of audit reports related to maintenance / equipment performance and follow up the closing out of such audits as deemed necessary.
Supervision
- Plan, supervise and coordinate all activities in the assigned area to meet functional objectives.
- Train and develop the assigned staff on relevant skills to enable them to become proficient on the job and deliver the respective section objectives.
Budgets
- Provide input for preparation of the Section / Department budgets and assist in the implementation of the approved Budget and work plans to deliver Section objectives.
- Investigate and highlight any significant variances to support effective performance and cost control
Policies, Systems, Processes & Procedures
- Implement approved Section / Department policies, processes, systems, standards and procedures in order to support execution of the Section’s / Department work programs in line with Company and International standards.
Performance Management
- Contribute to the achievement of the approved Performance Objectives for the Section / Department in line with the Company Performance framework.
Innovation and Continuous Improvement
- Design and implement new tools and techniques to improve the quality and efficiency of operational processes.
- Identify improvements in internal processes against best practices in pursuit of greater efficiency in line with ISO standards in order to define intelligent solutions for issues confronting the function.
Health, Safety, Environment (HSE) and Sustainability
- Comply with relevant HSE policies, procedures & controls and applicable legislation and sustainability guidelines in line with international standards, best practices and ADNOC Code of Practices.
Reports
- Provide inputs to prepare Section MIS and progress reports for Company Management.
5. COMMUNICATIONS & WORKING RELATIONSHIPS:
Internal
External
6. QUALIFICATIONS, EXPERIENCE, KNOWLEDGE & SKILLS:
Minimum Qualification
- Bachelor Degree in Electrical/Mechanical Engineering Discipline or equivalent.
Minimum Experience & Knowledge & Skills
- 10 years of experience in maintenance activities, including 5 years in reliability activities in oil and gas.
Professional Certifications
7. TECHNICAL COMPETENCIES:
- As per the approved ADNOC Competency dictionary
8. behavioural CompetenciEs:
- As per the approved ADNOC Competency dictionary
تفاصيل الوظيفة
- منطقة الوظيفة
- أبو ظبي, الإمارات العربية المتحدة
- قطاع الشركة
- خدمات الدعم التجاري الأخرى
- طبيعة عمل الشركة
- صاحب عمل (القطاع الخاص)
- نوع التوظيف
- غير محدد
- الراتب الشهري
- غير محدد
- عدد الوظائف الشاغرة
- غير محدد